How to diagnose and prepare problem concrete surfaces.
Concrete is one of the oldest building materials, dating back to the Romans in 100 B.C. Like the Romans, today's building and heavy construction industry still relies on concrete's strength. Unlike the ancients, modern trade professionals now have more tools to help extend the life of concrete surfaces.
Larry Mroz, business development manager for the concrete products group at Sherwin-Williams, periodically teaches a continuing education course for the American Institute of Architects (AIA) that helps professionals understand basic concrete composition, diagnose problems, handle surface preparation and repairs, and specify the right protective coatings for projects. Here's a capsule summary of that course:
Concrete: The basics
The word "cement" is often mistakenly used to describe "concrete." But Portland cement is just an element of the concrete mixture. When mixed with water, Portland cement becomes a workable paste. The lower the water content, the stronger the finished concrete will become. During the mixing process, aggregates (such as gravel, crushed stone or sand) are added to improve concrete strength and durability. Typically, aggregates make up 60 to 75 percent of overall concrete volume.
In addition to standard aggregates, concrete can contain polymer additives, which can improve a surface's flexural strength while reducing shrinkage. In certain applications, corrosion inhibitors are used to extend the life of embedded rebar supporting horizontal and vertical structures.
The type of aggregates and additives in concrete are usually defined by the end use. For example, a fine sand aggregate is often used for vertical or overhead applications. On the other hand, deeper pours on horizontal surfaces (such as sidewalks or concrete driveways) need a coarse aggregate mixture.
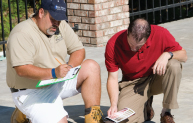
Diagnosing damage to existing concrete
The forces that cause concrete problems fall into three basic categories:
Internal forces may include concrete shrinkage from natural drying, a poor-quality initial mixture or inadequate curing.
Human forces can involve a wide range of issues, such as weight overloads, sharp impacts or the use of certain chemicals on concrete surfaces.
Environmental forces are often freeze-thaw cycles, wind-driven rain or "acts of God" — such as fires, floods or earthquakes.
When beginning a condition survey, the most obvious starting point is a visual inspection. This would include checking horizontal or vertical surfaces for significant cracking or scaling or pop-outs (due to freeze-thaw, chemical attack, porous aggregate [pop-outs], de-icing salts, poor quality concrete mix or improper finishing). These clues are the initial evidence that the concrete substrate may not be sound.
When a visual inspection doesn’t provide enough information on problem and treatment, consider these two follow-up steps:
Nondestructive testing. A common nondestructive test involves dragging a heavy chain across a horizontal concrete surface and using a petrographic meter to listen for soundings in the hollows of the substrate.
Destructive testing. This more aggressive diagnostic tool often requires drilling into concrete surfaces to obtain core samples, which are sent to a lab for chemical analysis. The analysis provides a scientific assessment of the substrate's condition and specific factors that are causing deterioration.
Many states require professional consultants or engineers when these tests involve structural repairs. However, even in locations where it's not required, contractors are strongly encouraged to use such professionals to ensure accurate test results, especially when structural elements are involved.
Proven protection
A brief sampling of top protective products from Sherwin-Williams:
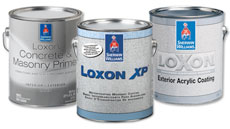
Loxon® Exterior Products. Our full line of exterior concrete and masonry solutions includes Masonry Conditioner, Block Surfacer, Acrylic Primer, High Build Coatings and Water Repellants. Loxon's elastic formula helps bridge hairline cracking and can be applied on hot (green or fresh) concrete, stucco and block surfaces with a pH of up to 13. Loxon's unique system allows the coating to resist efflorescence and wind-driven rain, providing a protective shield against moisture and mildew.
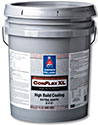
ConFlex XL™ High Build Coating. This elastomeric waterproofing coating protects concrete and masonry surfaces from water penetration and is available in smooth or textured finishes. Its thick, elastic film covers, hides and protects — minimizing pinholes and bridging cracks. Use it confidently on all types of new construction or repaints, including concrete panel, pre-cast concrete panel, CMU and stucco.
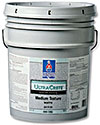
UltraCrete Texture Coating. Trust this coating to provide an attractive, economical, uniform textured finish for masonry substrates and enhance the appearance of tilt-up, CMU construction or precast panel surfaces. It minimizes surface irregularities and imperfections for a handsome presentation with good color retention. UltraCrete is available in fine, medium or extra-coarse textures and a variety of custom tints.
Preparing and repairing concrete surfaces
When preparing concrete surfaces for application of protective coating or sealants, it's important to choose the right approach for the job. This can range from basic pressure washing to very aggressive mechanical abrading techniques.
Concrete porosity — or surface absorbency — is critical to ensure proper coating adhesion. On horizontal surfaces, a good way to assess porosity is the "dime rule." Place a dime-size water bead on the concrete and time the rate of absorption. If this test takes 15 to 20 seconds, then power washing or a phosphoric acid etch should be enough to open concrete pores. Conversely, if the water takes a minute or more to disappear, the surface may require diamond grinding, abrasive blasting or scarification to provide adequate absorption.
Preparation of vertical surfaces requires more careful consideration. Acid etching is not recommended, due to application difficulty and spillage concerns. Similarly, it's wise to avoid mechanical grinding on vertical surfaces, largely due to the risks of silicosis (a respiratory disease caused by silica dust). In fact, the most common technique for walls and other upright concrete areas is pressure washing. In cases requiring more aggressive surface preparation, sandblasting is an acceptable procedure.
Protective concrete coatings: Managing customer expectations
When it comes to selecting coatings, a trade professional must often walk the line between managing customer expectations and choosing the right product for a specific job.
In recent years, as the national economy still seeks to regain momentum, many commercial and residential property owners are continually looking to do more with less. In terms of protective coatings for concrete surfaces, that often means selecting a middle-of-the-road product, which delivers good — but not maximum — return on investment.
"Asking good customer questions, and really listening to their responses, is a critical element," Mroz says. "The bottom line is that you need to have a ‘good-better-best' product continuum in your recommendations." For example, if the customer wants a long-term protective solution, you need to stress the benefits of that higher-quality product and how the upfront higher cost will result in less expense over time.
Concrete Know-How:
Continuing education programs from Sherwin-Williams keep you up to date on concrete coatings techniques and information. Call 1-800-524-5979 to have a sales representative contact you.